Chopping It Up With OAR Woodworks

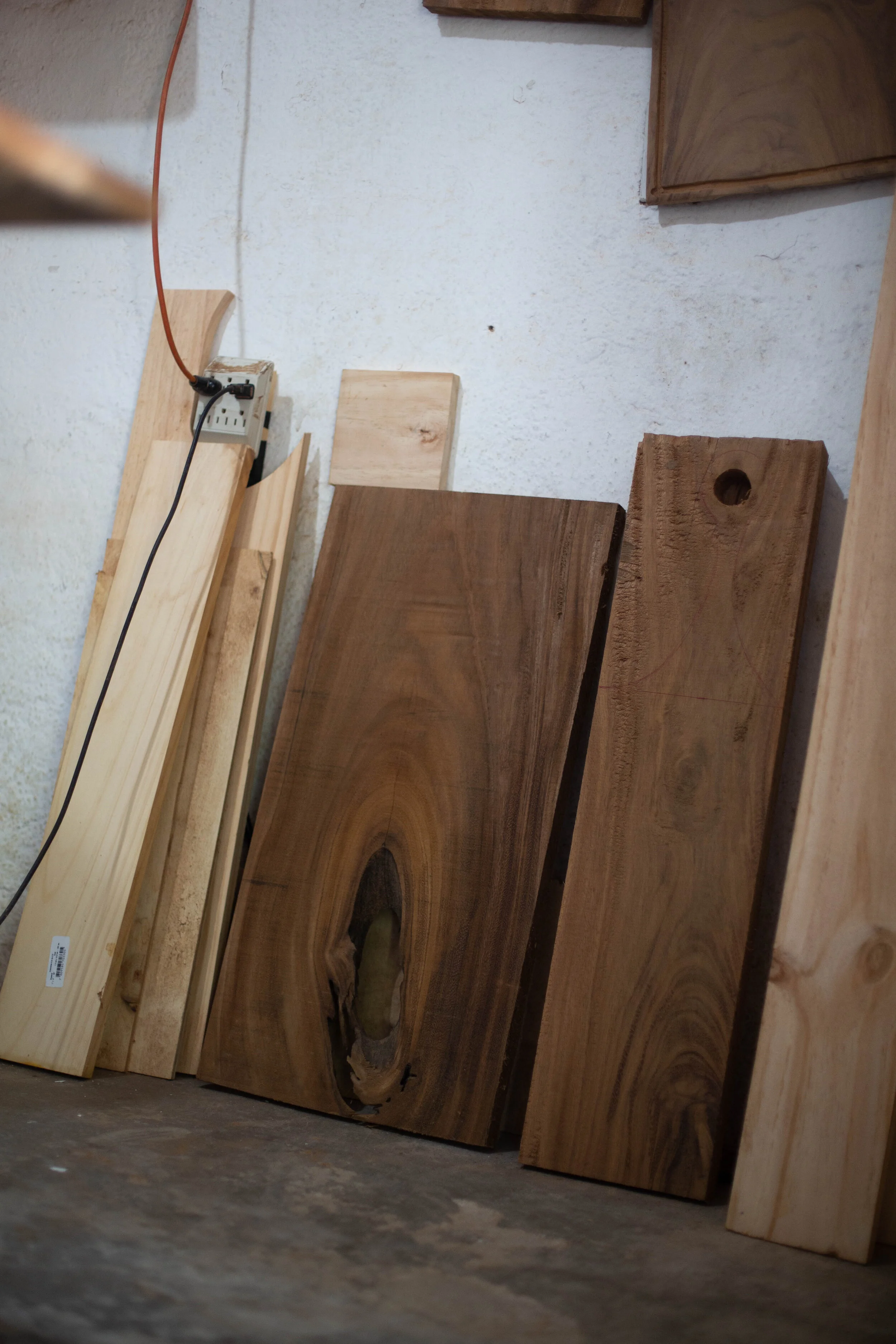



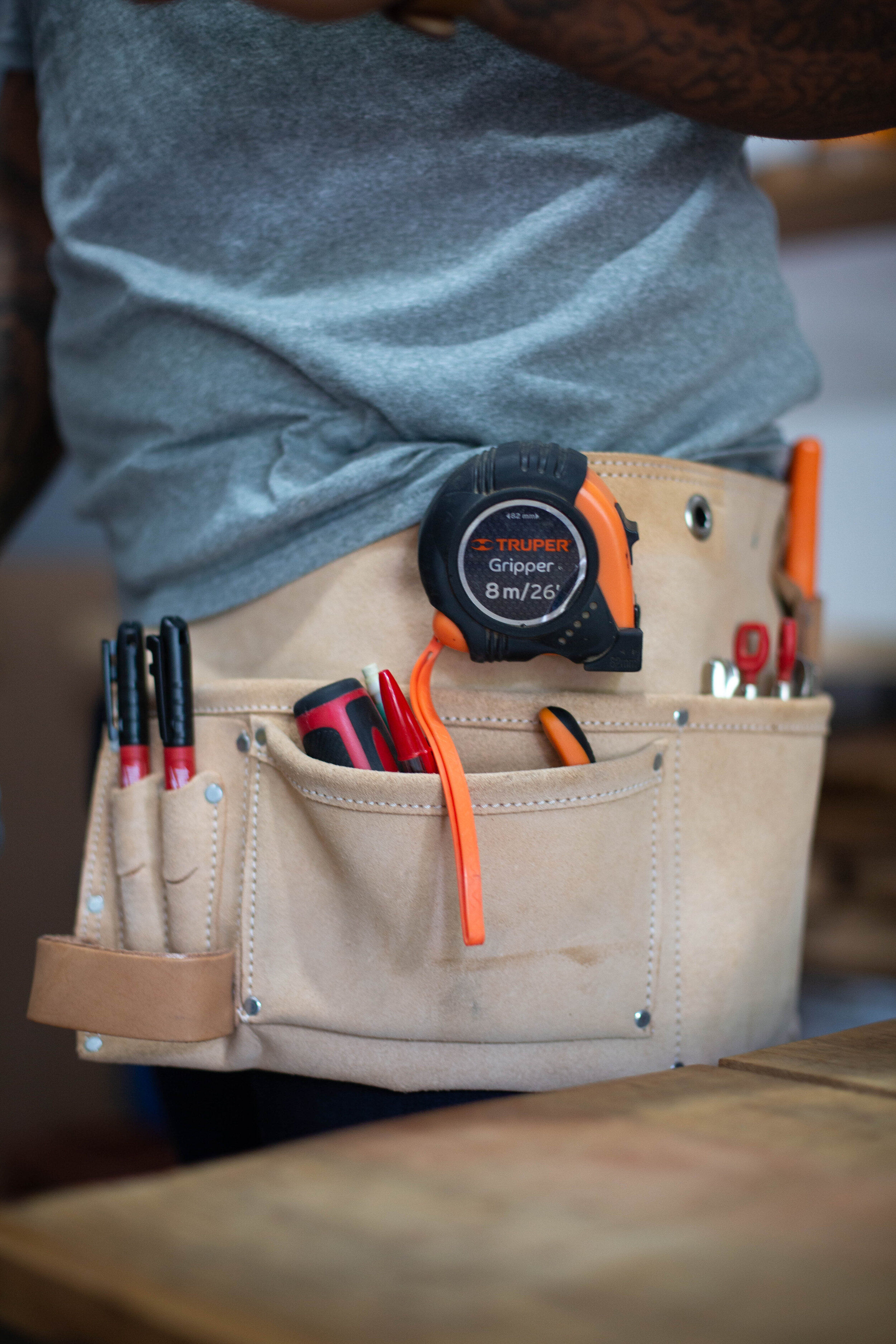
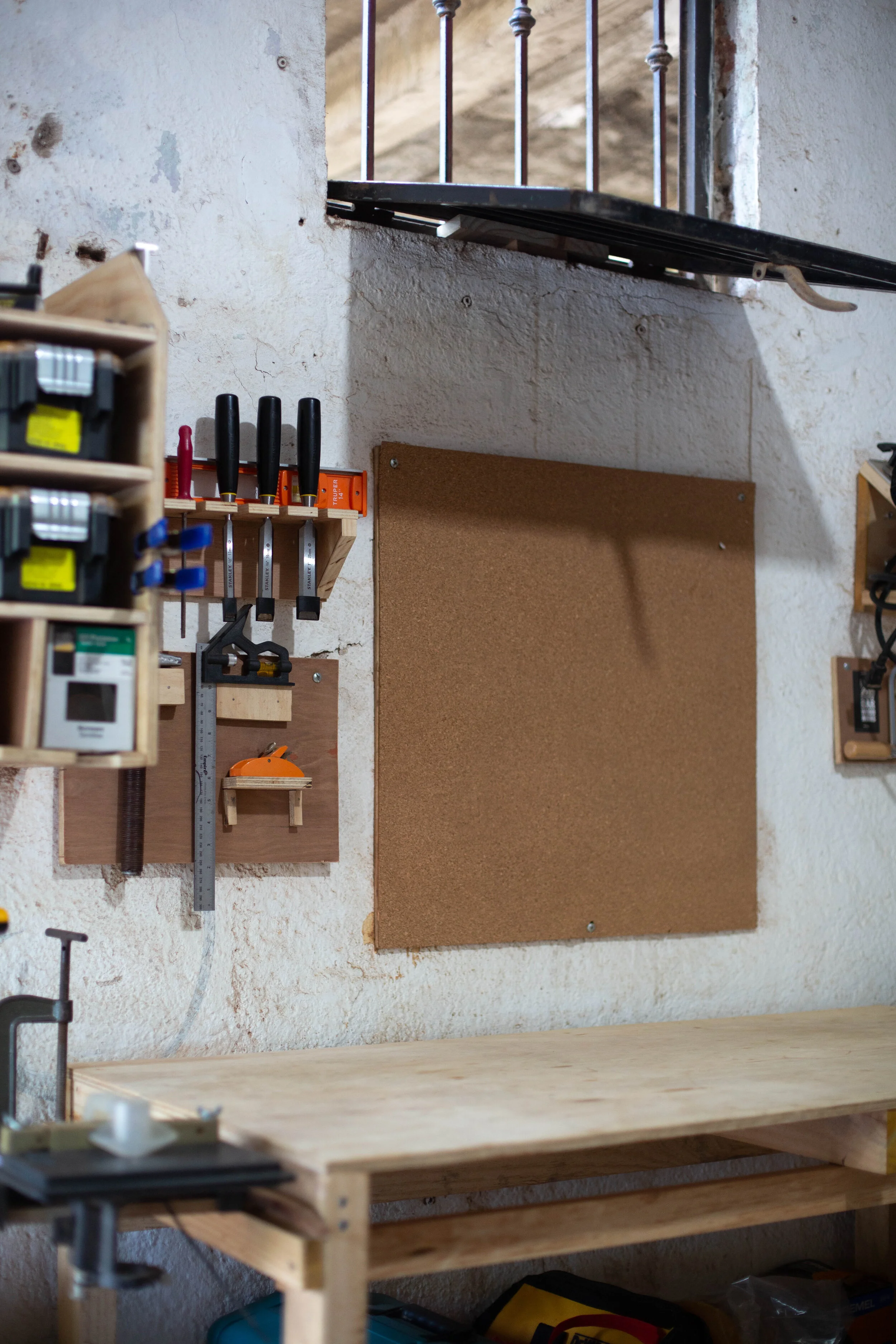

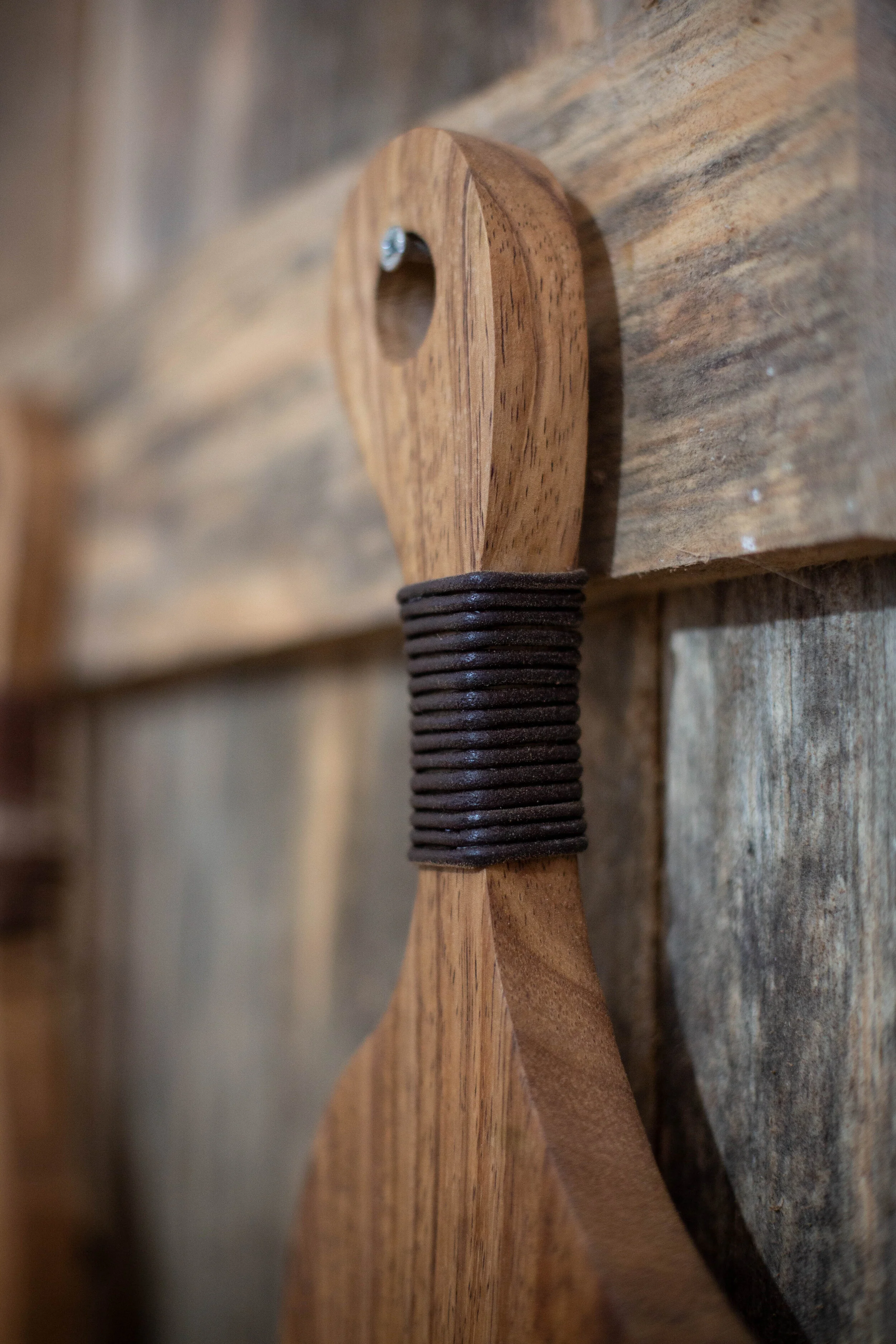
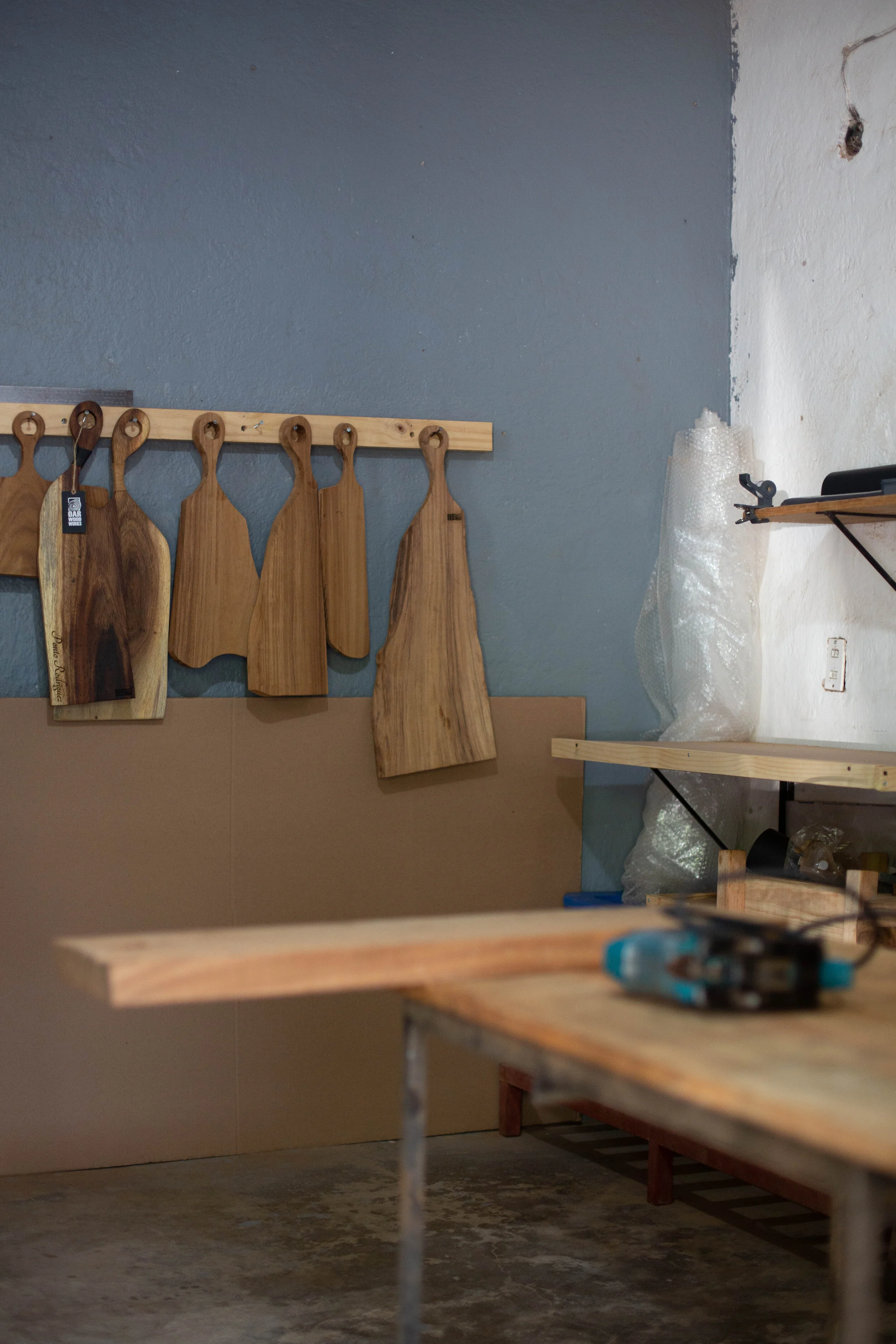

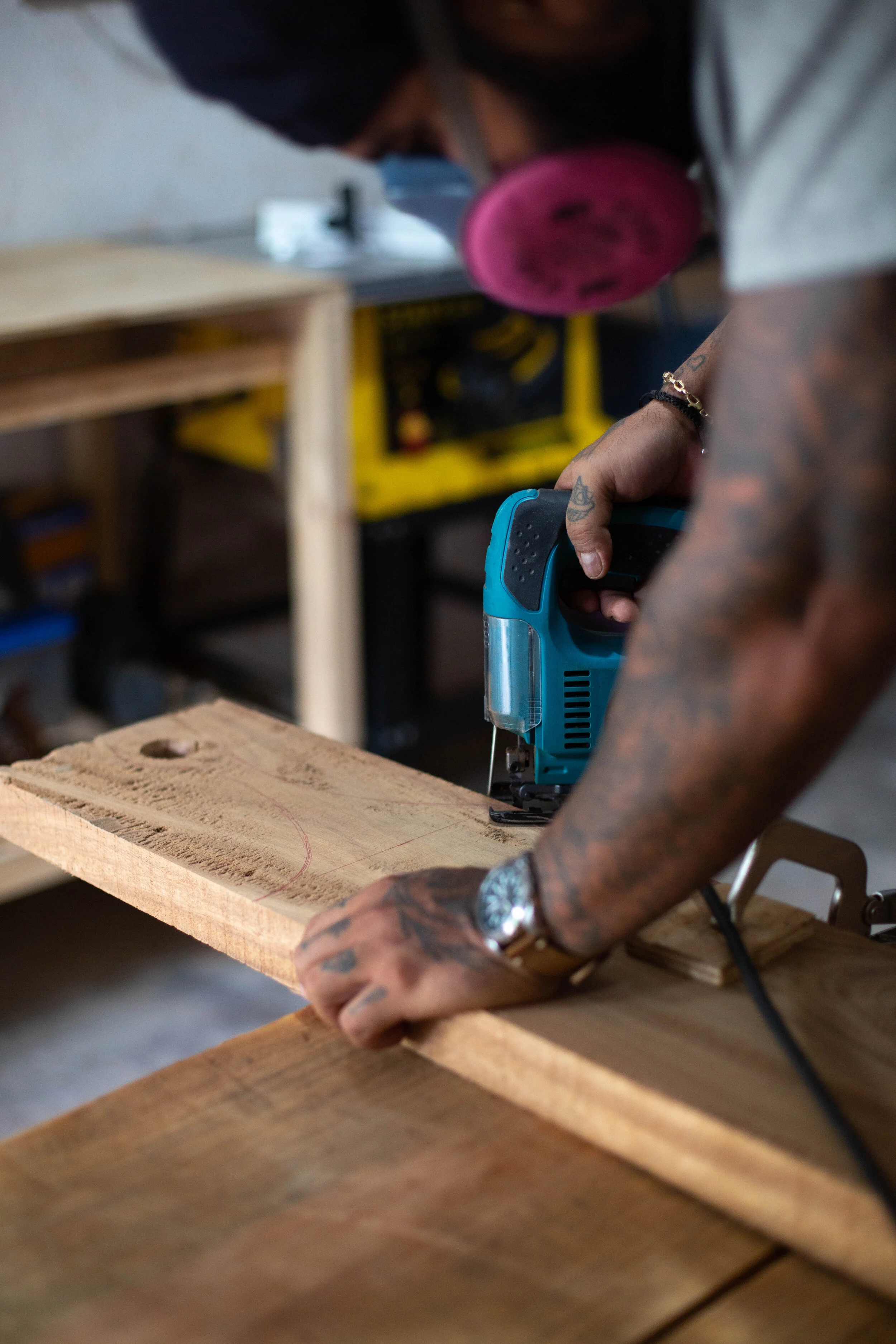



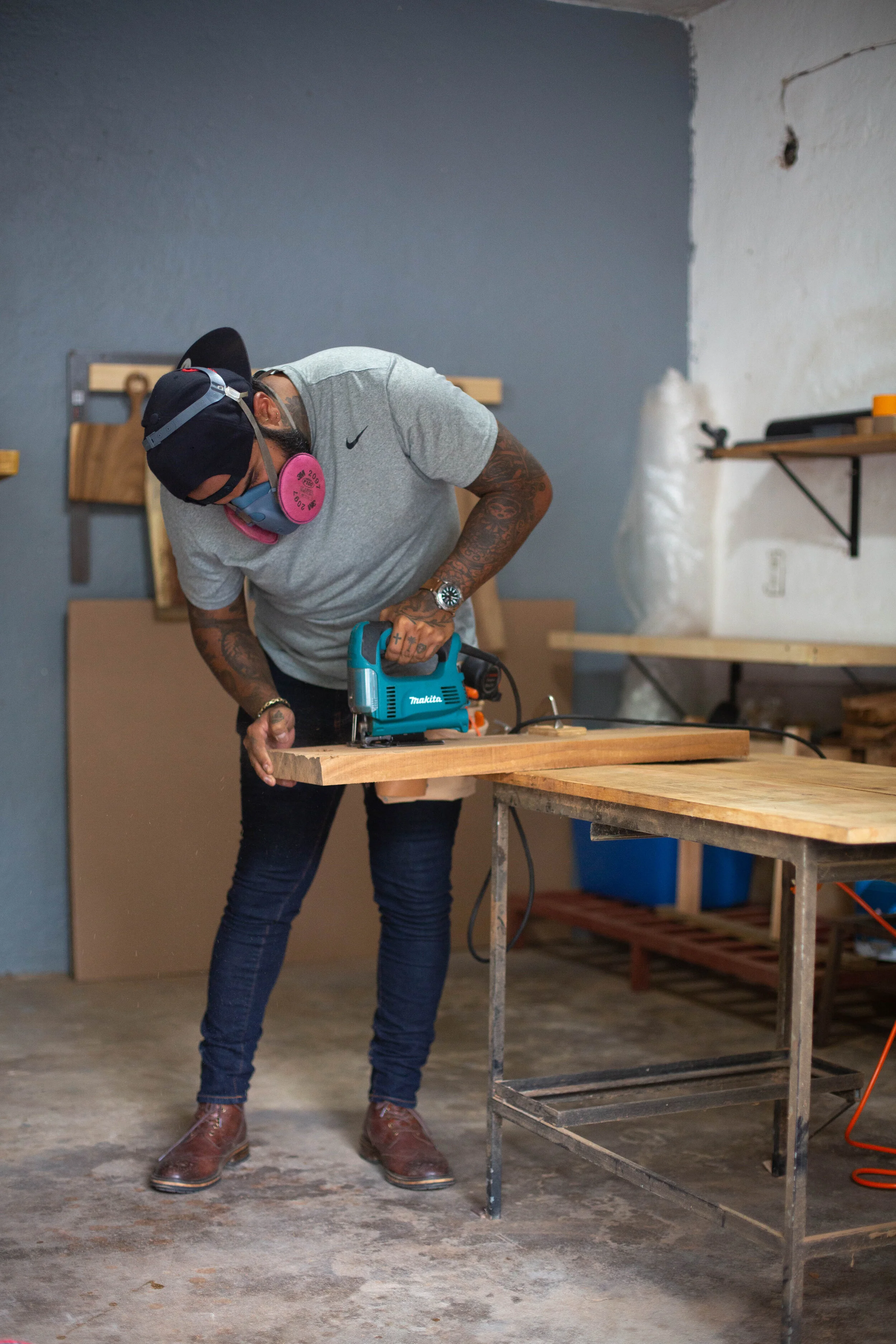


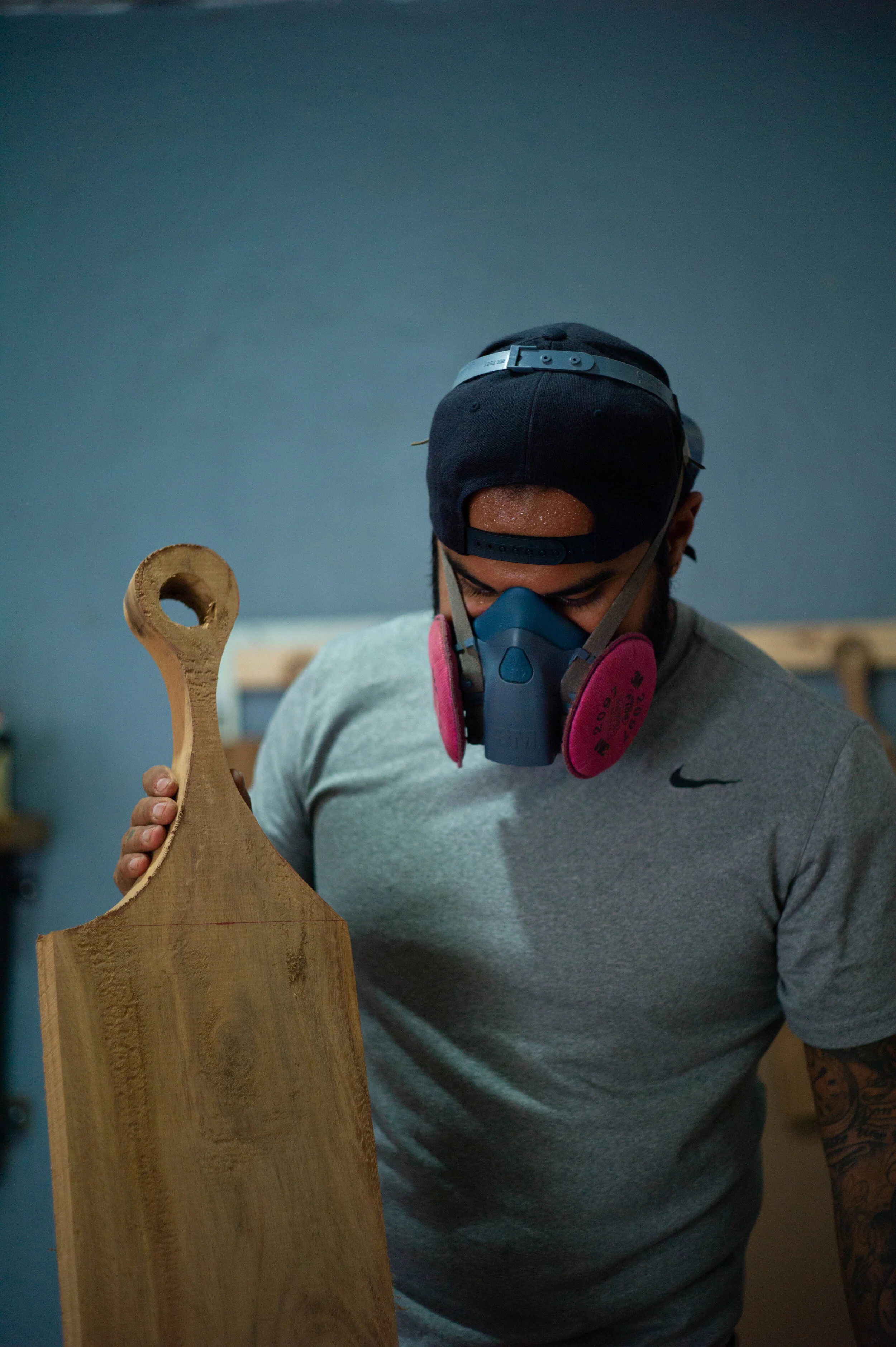
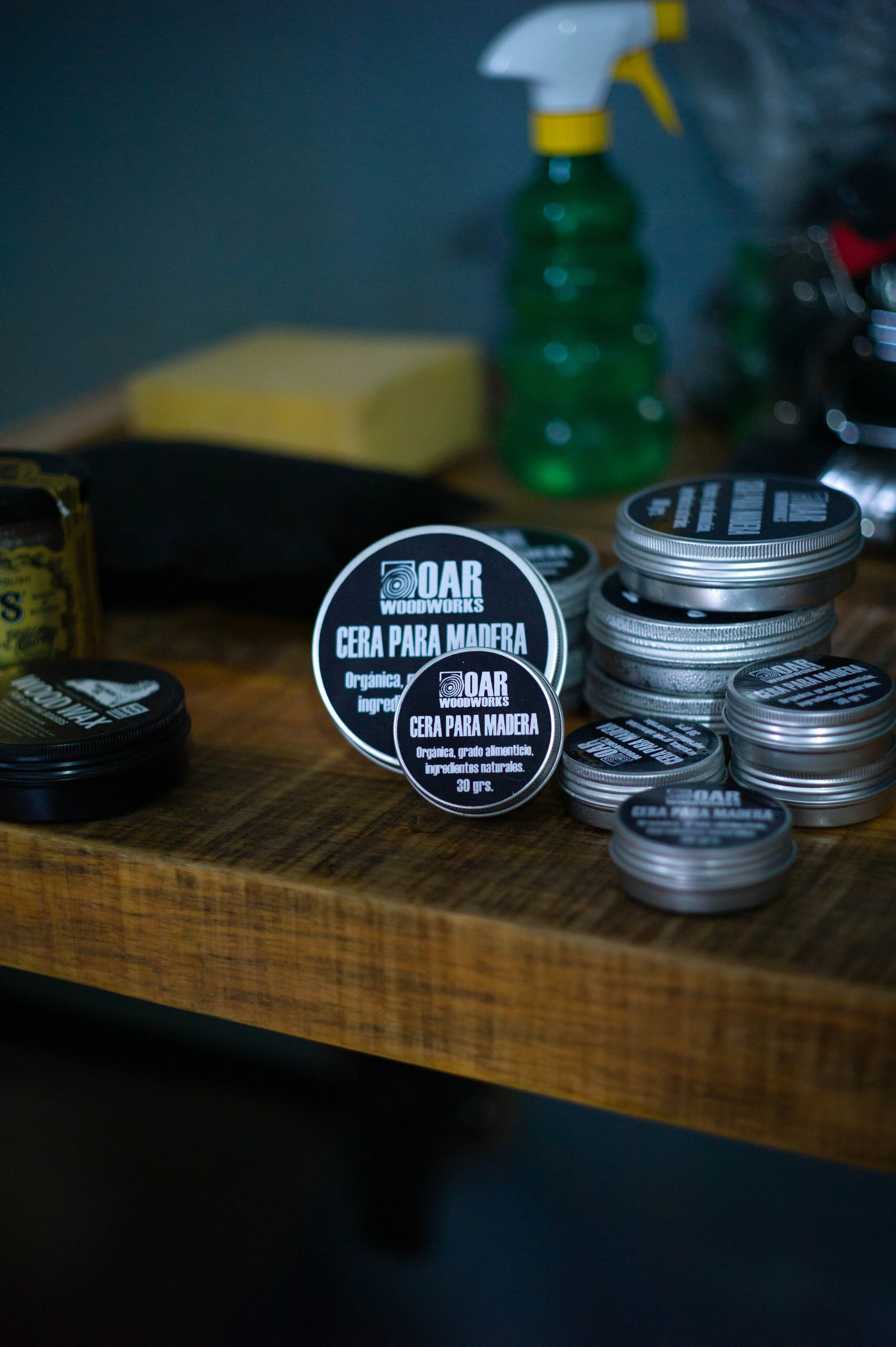
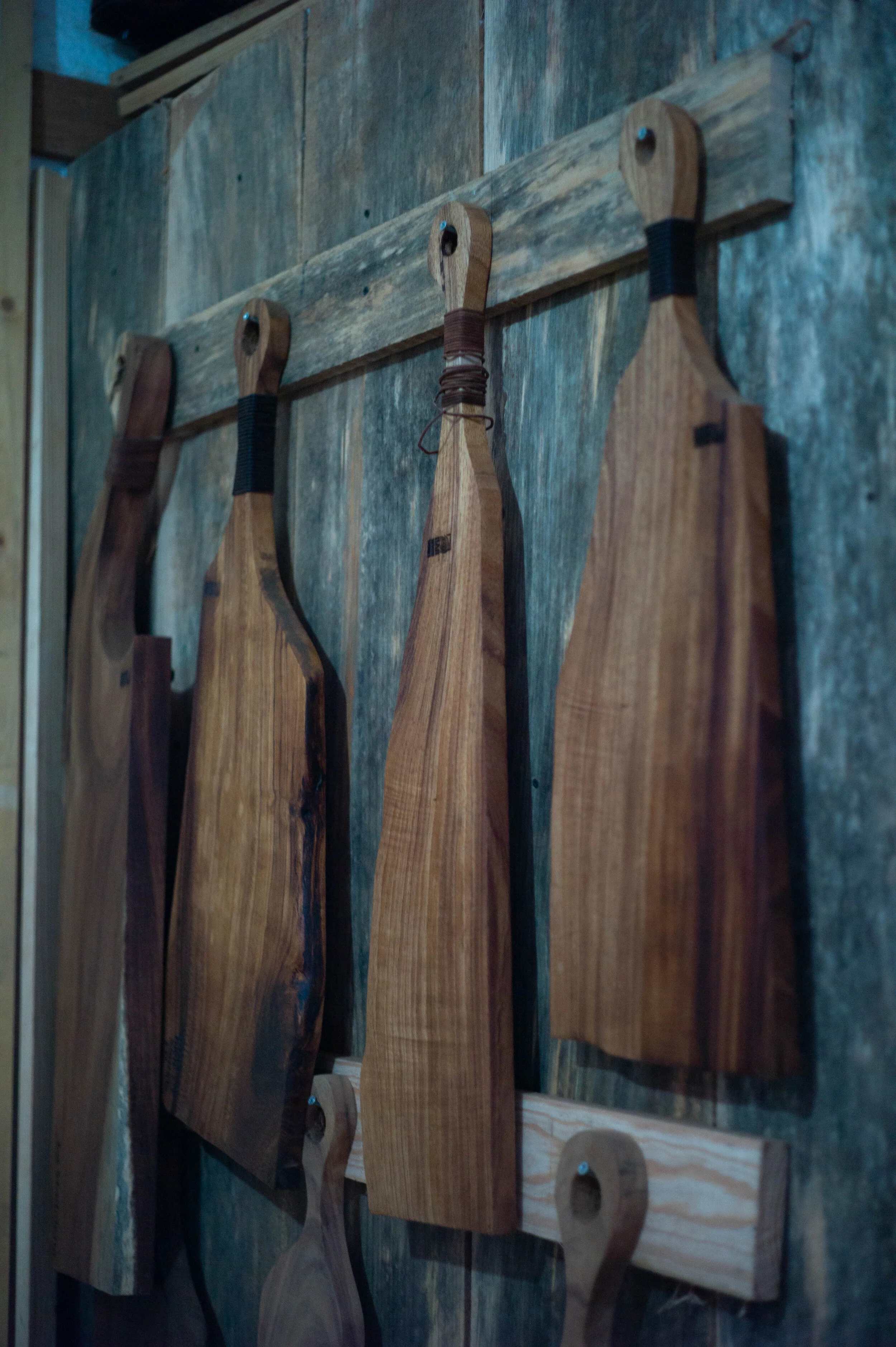

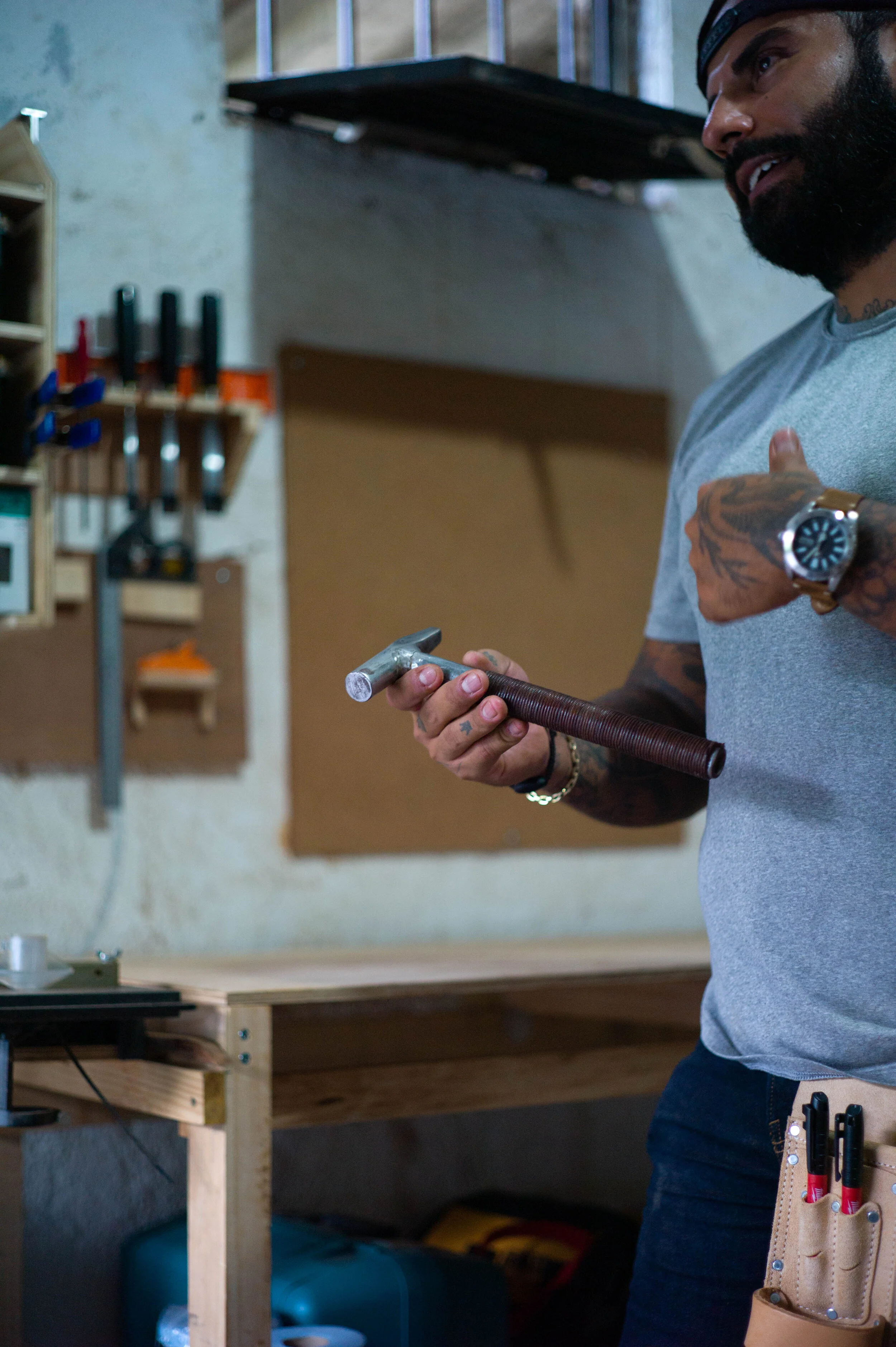
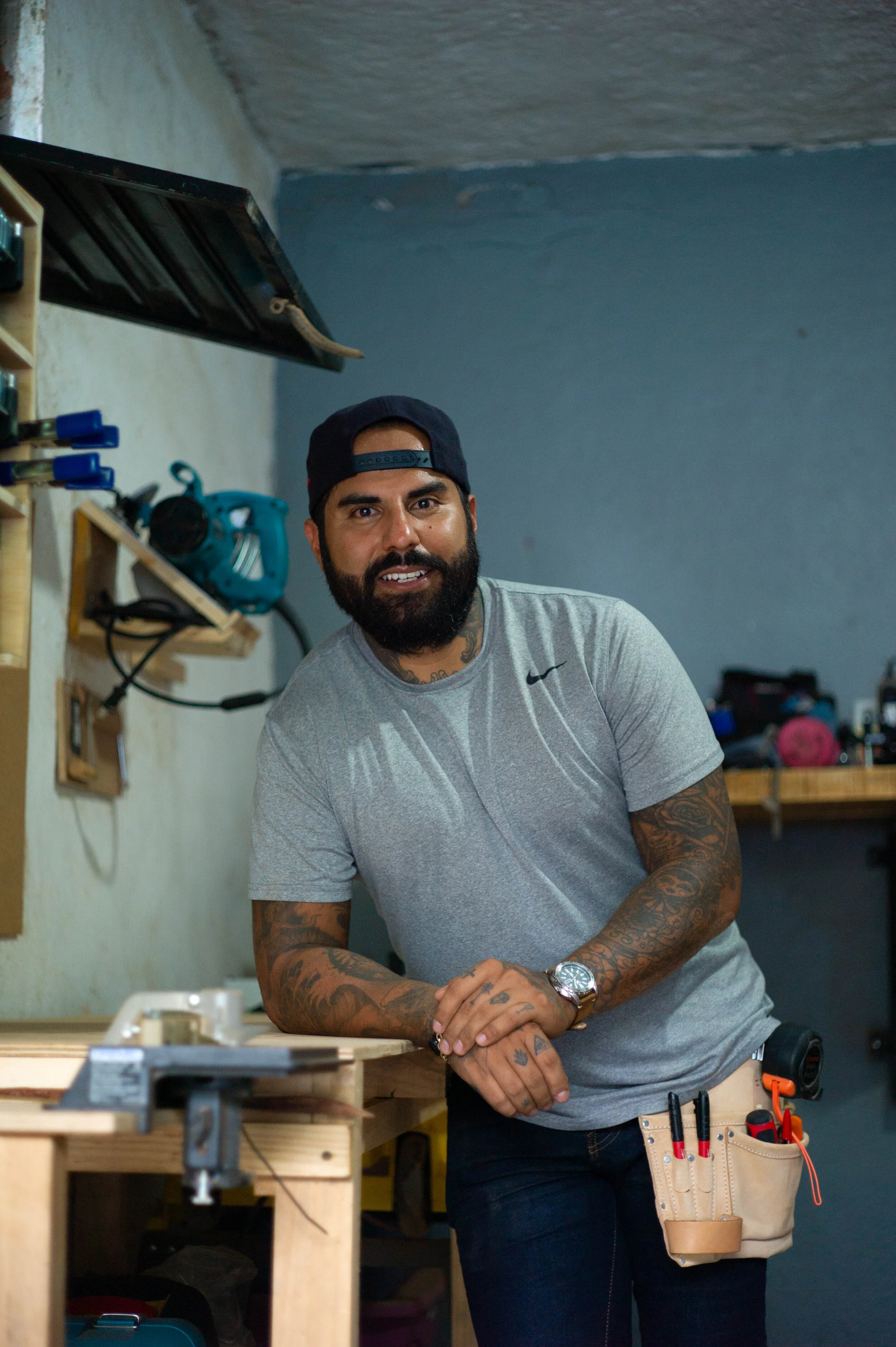

Written by Jesse
With so much time [and boredom] on our hands, a lot of amazing ideas and businesses were born out of quarantine. Among those was OAR Woodworks. A small business specializing in wooden boards that serve a number of uses, such as cutting boards or cheese and meat serving platters, it has taken Vallarta by storm. One of a kind, OAR Woodworks is a niche market that is few and far in Vallarta. Owned by Orvin Ramos, OAR is of the highest quality when it comes to woodworks for your home, whether it be for decor or for working [or serving] in the kitchen.
As you enter Orvin’s workshop in Bucerías, you immediately notice it’s small size. There is a film of coarse dust that gently falls over and covers every inch of his workspace; the kind of dust that comes only from sand dusting wood. Tiny, hot and full of dust, you wonder how Orvin can create such magic there. But he does. In fact, it is the perfect space; and don’t get me wrong, his workshop had my heart from the second I saw it. It is quaint, extremely organized, and well kept.
As I watched Orvin at work, I quickly realized that this man could create magic in any location, in any environment. The passion, the skill, the effortless talent that Orvin possesses is unparalleled. It’s as though he’s been doing this his whole life, and get this -- it’s only been 6 months. As I watched him I was truly amazed at how well he has mastered such a difficult craft.
Talking about his boards, Orvin oozes excitement. You want to buy one without even seeing what they look like, the passion in his eyes says it all. And of course, when you see the finished product, you are immediately sold. From the finishing to the details, they are flawless. The leather strap on the handle screams luxury while the little feet on the bottom allow for functionality.
After an informative photoshoot and chit-chat about the business, we sat down to talk with Orvin about OAR and the whats, the whys and the hows. Read our interview below!
----
Jesse: Talk to me about your process and how you get from point A to point Z with your boards.
Orvin: Let me show you. I don’t have much wood right now, as I’ve used most of it and am waiting for more. But I’ll take a board like this [picks up a long, rectangular piece of wood], I draw the shape I want to cut, all free hand. First to go is the handle. I draw that and cut it before doing the rest. I cut it both the handle and board out with a tool that is called the jigsaw. The shapes and sizes differ a little each time. After that, comes the sand dusting which is a super long process. I start with an 80 grind which is pretty thick and I finish with 320 which is a super fine grind. After sand dusting with the machine, I finish the sand dusting process by hand with a 400 grind and later with a 600 grind. They are really fine grinds and ensure that the board is left extremely smooth. That’s how I do the finishing. Between the 150 and 220 grind I put water so it can embrace the grain of the wood. And that’s so that when you use your board and go to wash it, the wood can sustain it.
J: Wow so this is a pretty intense process, huh?
O: Oh yeah, you need to have a cooler with water or beers and you are sweating all day. It’s hard work.
So once the board is smooth and the sand dusting process is over, we put the oil, leave it on for 24 hours, move the excess and apply the wax. And with that, the board is ready!
In one complete day, when I start working at 10am, I can finish cutting and dusting 8 boards. From this [points to long piece of wood] to this [points to finished board].
J: That’s fantastic! And the leather piece around the handle comes at the end?
O: The leather actually comes after the last sanding, before the oil. And before the leather, I screw on the little feet to the bottom of the board.
J: How do you stay organized in such a tight space with so much activity going on?
What I try to do is have stations. At this station [points to the table in the middle of the room] is where I draw and cut the wood. And then here [points to a table against the wall] I do the sanding, I put the leather and the feet. This wall is where I hang the boards I’m still working on and on this wall [points to the adjacent wall] is where I hang the finished boards.
This table is where I do the wrapping. The wrapping depends on where it’s being delivered. If I deliver it somewhere here in Vallarta, I just wrap it in paper. Delivering it in a presentable manner is very important.
If the delivery is for out of state, I wrap it in bubble wrap and cardboard.
J: Do you have a lot of orders from out of the country, out of state?
O: Yes! Actually the majority of them go outside of Vallarta. A lot to Leon, Monterrey, a lot of Northern states where Carne Asada is more prevalent.
J: What type of wood do you use?
O: Parota, just parota. It’s a wood native to Mexico that is very noble. It has beautiful colors, and of course is anti-termites.
J: How did OAR Woodworks get started?
O: It originally started because I was going to make these organic gardens for homes. This was the initial idea when I realized I had too much time on my hands due to quarantine. This little place [Orvin’s workshop] was full of my bicycles, motos, etc… There was a lot of stuff here, but I had a space to create. So, I said ok I’m going to do something and that was when my girlfriend, Lily, told me she had met a guy who was selling these big pieces of parota. So I said ok let’s buy some. We bought them and they were super rough, full of holes. I didn’t know what to do with them so I thought ok what can I do with these? What can I create with this wood?
The first boards were sand dusted by hand, because I didn’t know there was a machine that could do that.
Once the wood had been dusted down, Lily tells me, why don’t you make platters for carne asada? And I thought to myself, wow what a great idea, there is nothing like this on the market. So I started creating them. Obviously the first board I made looks much different than the ones I have now. At first I was just learning, and they came out skinnier and different in shape. I didn’t have the little feet that I now put on them nor the details that they have now. Now they are a lot prettier and are better quality.
J: Do you have any upcoming projects or collaborations?
O: October is breast cancer awareness month so I’m going to make only a few exclusive boards to sell. Of course, all proceeds will go to a breast cancer foundation and charity. What makes these special is that the leather on the handle will be pink. The colors of the wood with the pink are going to look amazing! And also, it feels good helping those in need. It’s a project I’m super excited about.
J: What has been the feedback of OAR Woodworks?
O: It started as a hobby and to be honest, I didn’t think people would want to buy them. The feedback has been off the charts! One woman yesterday told me “I unwrapped the board and it is so beautiful, I don’t want to use it, I just want to look at it and admire the beauty.” I have not had one person who wasn’t happy with their purchase. No one wants to use them because they like them so much, but obviously I want people to use them without being scared that something will happen! They’re built to last!
J: They definitely are! How did you think of the name OAR Woodworks? Your name is Orvin, so did it come from that or did you think of and were inspired by an actual oar?
O: OAR actually is my initials, Orvin Antonio Ramos. But how funny, because one of my friends had told me that oar in english is a wooden paddle used for rowing. That wasn’t my intention or inspiration for the name OAR Woodworks, and actually I had never before heard of an oar. When I created the name, I didn’t think it would become a business. But here we are. The only thing I’m worried about is that “Woodworks” is hard to say if you’re a native spanish speaker and don’t speak english, so I’m thinking of changing the name. In english I love the name but I’m not so sure it works in spanish.
J: Well, it’s no coincidence that your initials (OAR) mean a wooden paddle exactly the same shape as the boards you create.
Talk to me about some of your goals for OAR. Where do you want to take it?
O: A long term goal would be that almost every home has an OAR Woodwork board. And a short term goal would be to get a bigger workspace. I want to produce more and maybe have someone to help me. There is only so much I can do in this space, only so much wood I can have in here, so a bigger workshop would be ideal!
My goal is to take OAR Woodworks worldwide!
-----
So whether you are looking for something to spice up your kitchen, a cutting board you can count on, a serving platter to impress your guests, or a restaurant looking for innovative plating options, OAR Woodworks has got you covered. Orvin is currently taking orders via direct message on Instagram and Facebook at @oarwoodworks. Give him a follow and put in your order today!
A big shout-out and thank you to Orvin and OAR Woodworks for taking the time to show us how it’s done!